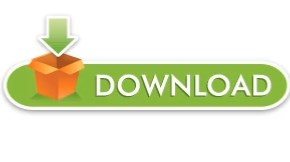

- #MODSCAN32 SOFTWARE MANUAL DRIVERS#
- #MODSCAN32 SOFTWARE MANUAL DRIVER#
- #MODSCAN32 SOFTWARE MANUAL CODE#
This object is displayed on the work area and is linked to the desired data point on the node.

#MODSCAN32 SOFTWARE MANUAL DRIVER#
#MODSCAN32 SOFTWARE MANUAL DRIVERS#
Visualization programs with MODBUS device drivers are available from i.e. When choosing suitable SCADA software, ensure that it provides a MODBUS device driver and supports the MODBUS/TCP functions in the coupler. The WAGO ETHERNET fieldbus node provides the required process input and output values. The use of SCADA systems includes the areas of visualization and monitoring, data access, trend recording, event and alarm processing, process analysis and targeted intervention in a process (control). It is a user-orientated tool used as a production information system in the areas of automation technology, process control and production monitoring. SCADA is the abbreviation for Supervisory Control and Data Acquisition. I For a selection of SCADA products, look under i.e. There is a wide range of process visualization programs, called SCADA Software, from various manufacturers. This chapter is intended to give insight into how the WAGO ETHERNET fieldbus coupler/controller can be used for process visualization and control using standard user software. 7.2 Visualization and control using SCADA software
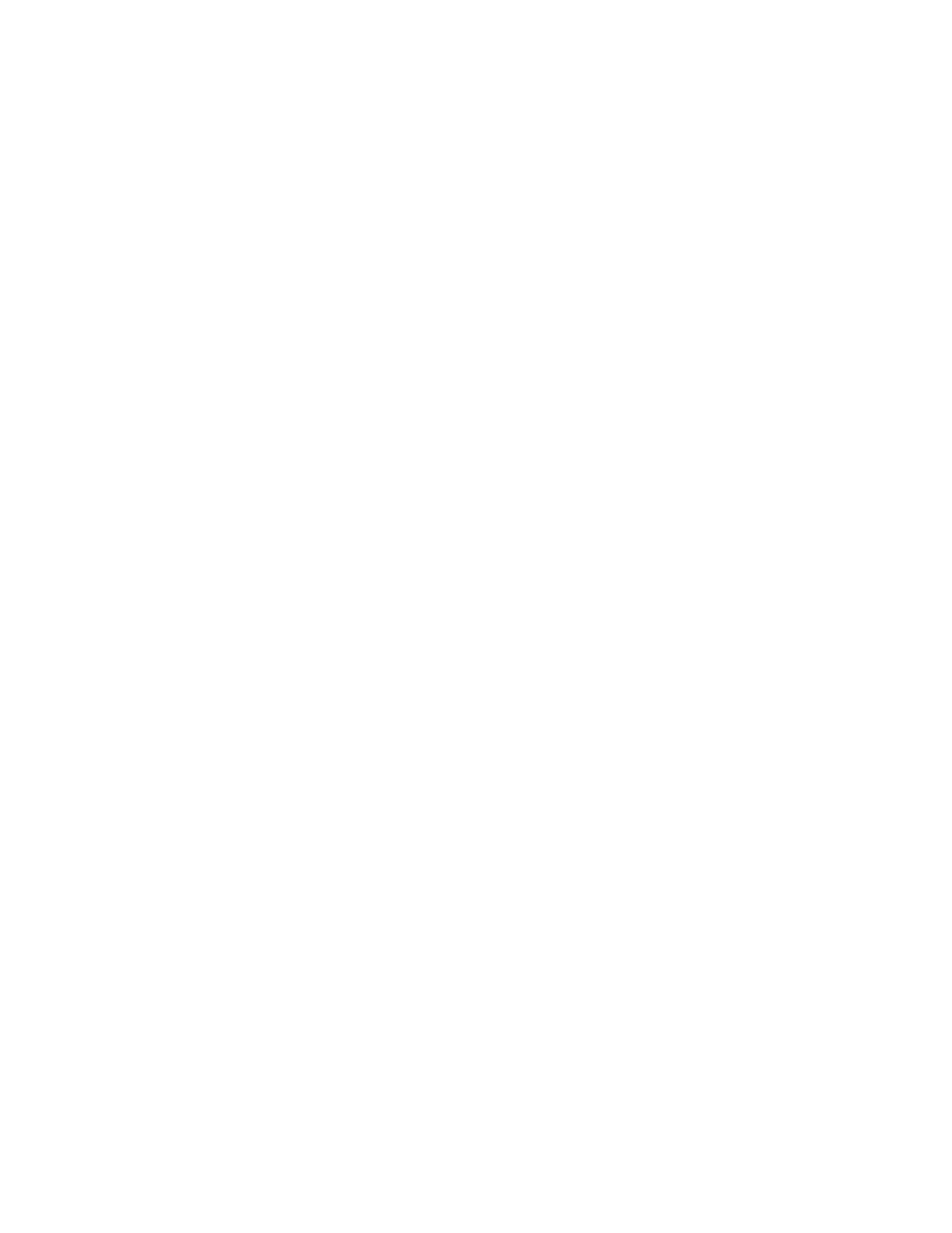
Visualization and control using SCADA software.Test of MODBUS protocol and fieldbus nodes.Special PFC Register (only for controller 750-842).
#MODSCAN32 SOFTWARE MANUAL CODE#
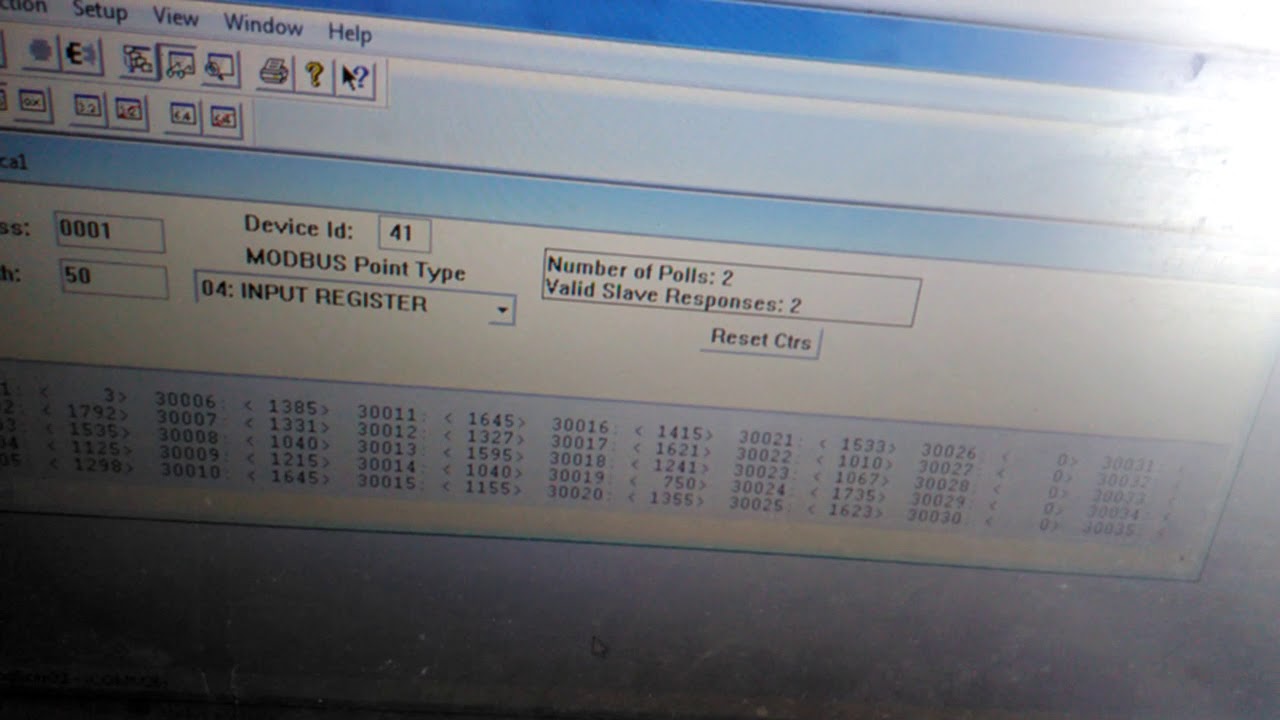
Reading out the information as HTML pages.Testing the function of the fieldbus node.Allocating the IP address to the fieldbus node.Starting up ETHERNET TCP/IP fieldbus nodes.Data exchange between MODBUS master and I/O modules.Process data architecture for MODBUS/TCP.
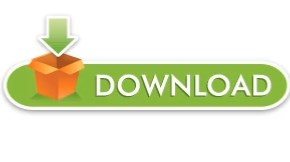